Traditional Roll Forming: A Comprehensive Guide
In the realm of metal fabrication, roll forming stands as a cornerstone technique, pivotal in shaping industries ranging from construction to automotive manufacturing. Among the various roll-forming methods, traditional roll-forming is a tried-and-true approach that balances cost-effectiveness, efficiency, and versatility. This article delves into the essence of traditional roll forming, exploring its mechanics, advantages, and diverse applications.
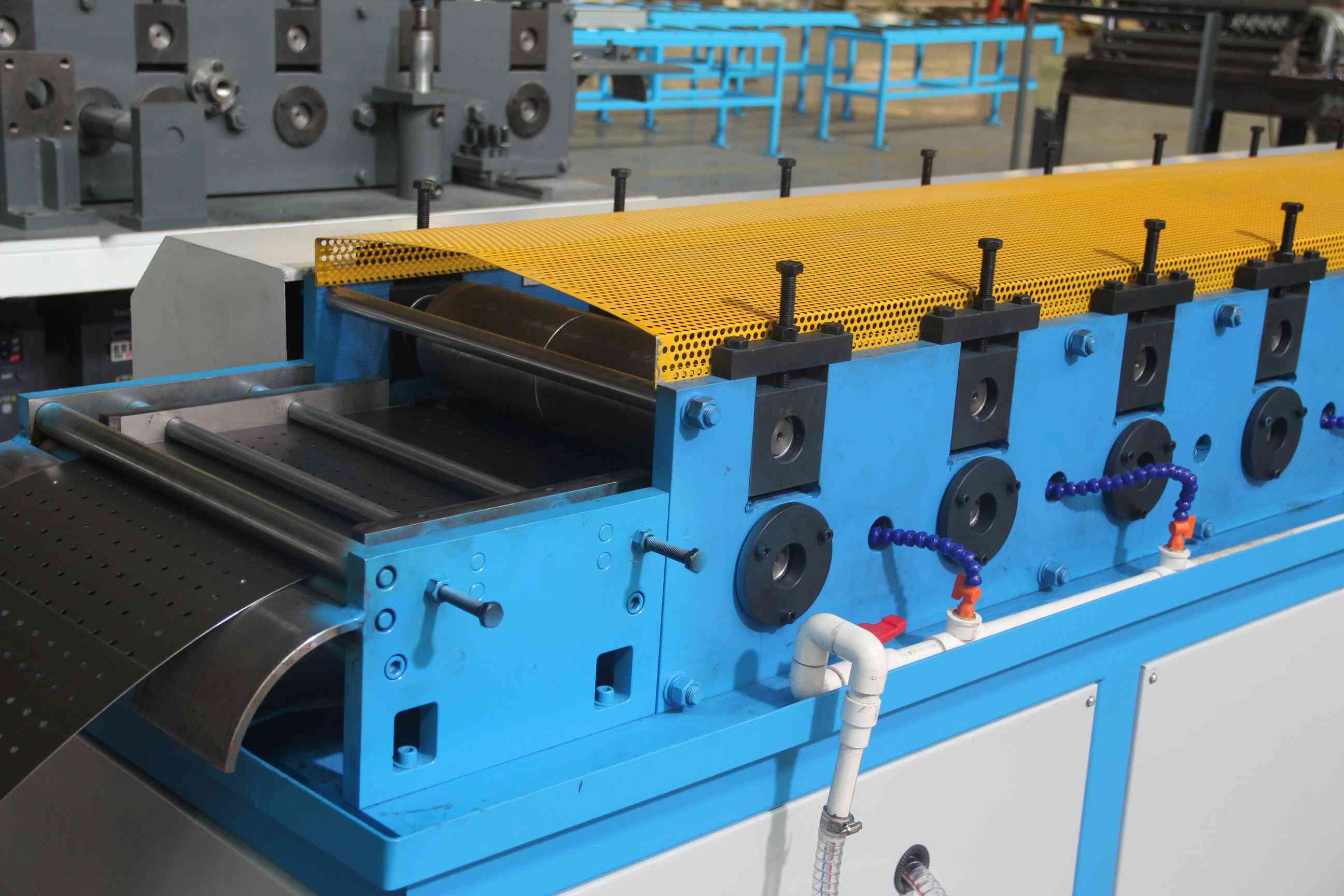
Understanding Traditional Roll Forming
Traditional roll forming, often referred to as conventional roll forming, is a continuous process that molds metal sheets or coils into specific cross-sectional profiles using a series of rotating rolls. Unlike other metal forming processes, roll forming excels in producing long, uniform sections with minimal waste, making it ideal for mass production.
The process involves feeding a metal coil into a roll-forming machine, where a sequence of precisely engineered rolls gradually shapes the material into the desired form. Each roll is designed with a specific geometry to ensure progressive deformation, resulting in a high-quality, consistent product.
The Mechanics of Traditional Roll Forming
- Material Preparation: The process begins with a metal coil, typically made of steel, aluminum, or other malleable materials. This coil is fed into the roll-forming machine, marking the start of the forming process.
- Roll Geometry: The precision of the rolls is paramount. Each roll is meticulously designed with a specific contour to progressively shape the material as it passes through. The sequence of rolls ensures that the material is gradually formed into the desired profile, achieving precise and consistent results.
- Continuous Shaping: One of the key advantages of traditional roll forming is its ability to operate continuously. This allows for the production of long, uniform sections without interruptions, enhancing efficiency and minimizing waste.
- Precision and Consistency: The roll-forming process is renowned for its ability to maintain tight tolerances. The precision of the rolls ensures that each piece of material is shaped to the same specifications, resulting in high-quality, consistent products.
- Post-Processing: After the material is formed, it may undergo additional processes such as cutting, finishing, or coating, depending on the application requirements.
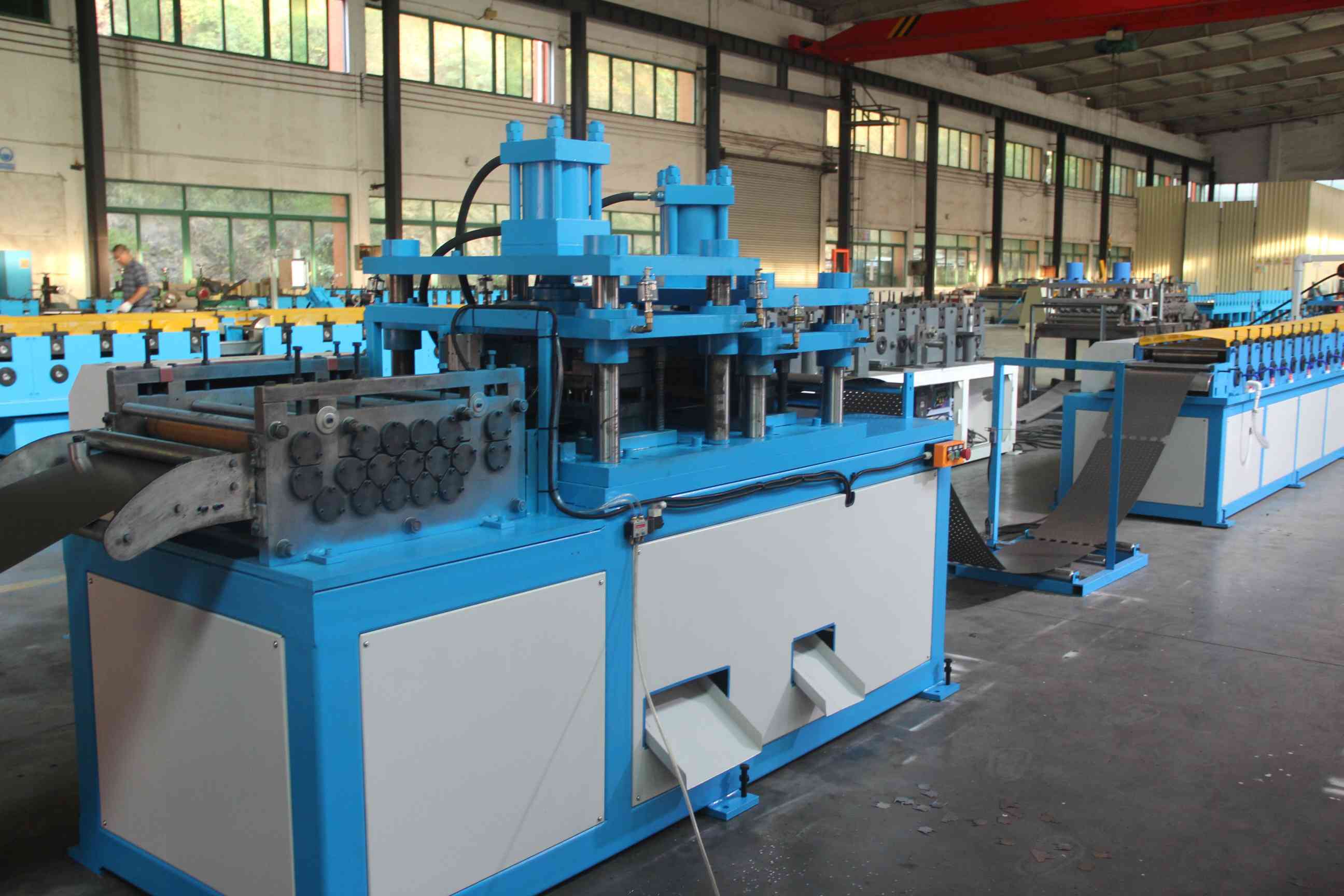
Advantages of Traditional Roll Forming
- Cost-Effectiveness: Traditional roll forming is a cost-efficient method due to its ability to process long lengths of material in a single pass, reducing material waste and minimizing production costs.
- High Precision: The use of precisely engineered rolls ensures that the formed profiles meet stringent quality standards, providing consistent results across all production runs.
- Versatility: This method is highly adaptable and capable of producing a wide range of shapes and profiles, from simple to highly complex geometries.
- Efficiency: The continuous nature of the process allows for high-volume production, making it ideal for industries requiring large-scale manufacturing.
- Minimal Waste: By shaping the material in a single pass, traditional roll forming reduces material waste, contributing to sustainability efforts.
Applications of Traditional Roll Forming
- Construction Industry: Roll forming is extensively used to produce structural components such as beams, columns, and roof profiles. These components are essential for constructing buildings, bridges, and other infrastructure projects.
- Automotive Industry: The automotive sector relies on roll forming to manufacture parts like car bodies, door panels, and chassis components. The precision and consistency of the process ensure that these parts meet stringent quality and safety standards.
- Manufacturing Industry: Roll forming plays a crucial role in producing components for machinery, appliances, and consumer goods. From household appliances to industrial equipment, the versatility of the process is invaluable.
- Aerospace Industry: In aerospace, roll forming is used to create lightweight yet durable components, contributing to the efficiency and safety of aircraft.
- Other Industries: The process is also utilized in the production of electrical components, furniture, and decorative items, showcasing its wide-ranging applicability.
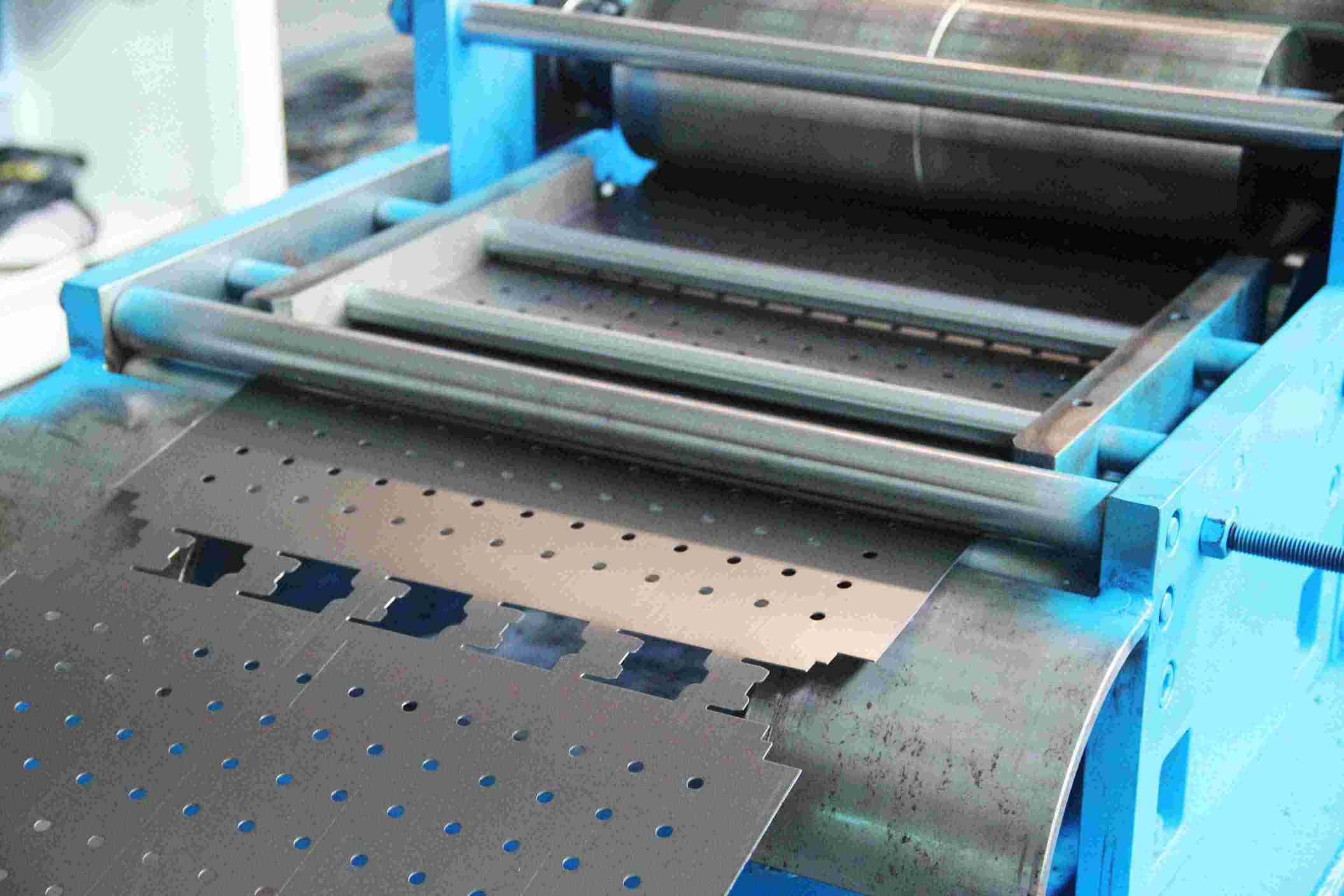
Challenges and Considerations
While traditional roll forming offers numerous benefits, it is essential to consider certain challenges:
- Initial Investment: The setup of roll-forming machinery requires a significant initial investment, particularly for custom-designed rolls and machinery.
- Design Complexity: The design of rolls and the forming process can be complex, requiring expertise to ensure optimal results.
- Material Limitations: While roll forming is suitable for a wide range of materials, it may not be ideal for extremely hard or brittle materials that are prone to cracking during deformation.
Innovation and Future Trends
The roll-forming industry is continually evolving, driven by advancements in technology and materials. Innovations such as computer-aided design (CAD) and simulation software have enhanced the precision and efficiency of the roll-forming process. Additionally, the integration of automation and robotics is revolutionizing the industry, enabling faster production and reducing human error.
Future trends are expected to focus on sustainability, with a growing emphasis on energy-efficient processes and the use of recycled materials. These developments will further solidify the role of traditional roll forming in modern manufacturing.
Traditional roll forming is a cornerstone of metal fabrication, offering a cost-effective, efficient, and versatile method for producing high-quality metal profiles. Its ability to handle long, continuous production runs and maintain tight tolerances makes it indispensable across various industries. As technology continues to advance, traditional roll forming will remain a vital process in shaping the future of manufacturing.
By understanding the mechanics, advantages, and applications of traditional roll forming, manufacturers can harness its potential to meet the demands of a rapidly evolving industrial landscape. Whether it's constructing skyscrapers, manufacturing vehicles, or producing everyday goods, roll forming will continue to play a pivotal role in shaping the world around us.